In the competitive packaging and printing industry, improving the efficiency of four color stack flexo printing machines requires a holistic approach. High-speed operations must balance productivity, precision, and stability, avoiding pitfalls like material deformation or inconsistent ink quality. Below is a streamlined strategy across five key areas:
1. Equipment Optimization and Maintenance
Enhancing speed begins with ensuring mechanical stability in stack type flexo printing machine. Regular replacement of high-precision gears and bearings minimizes vibration during high-speed runs. Upgrading servo motors and tension control systems maintains uniform material tension across unwinding, printing, and rewinding stages, preventing stretching. Laser calibration for printing pressure adjustment and dynamic balance correction of plate rollers reduce registration errors. Simultaneously, upgrading drying systems—such as adopting high-power LED-UV curing or optimizing hot-air circulation—ensures faster ink curing to support accelerated production.
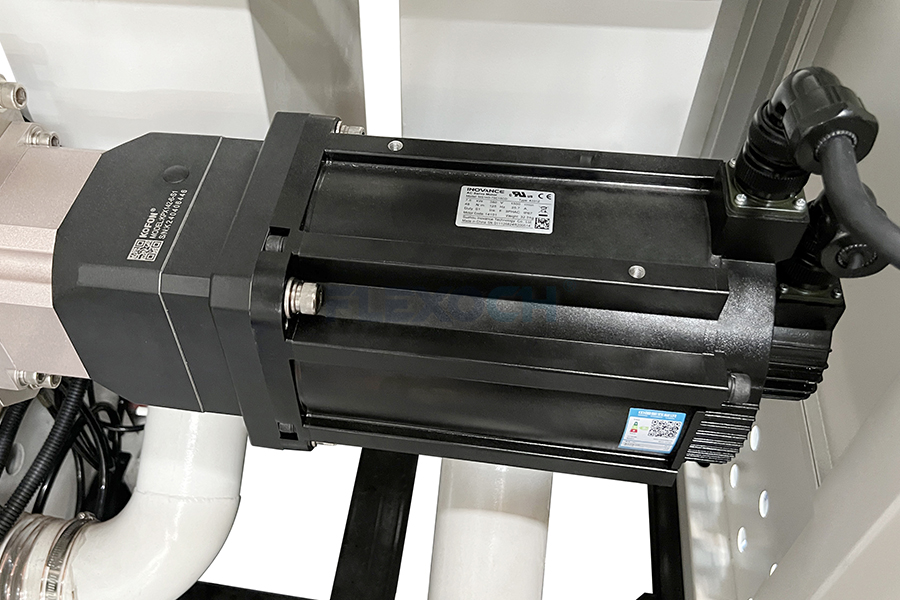
Servo Motor
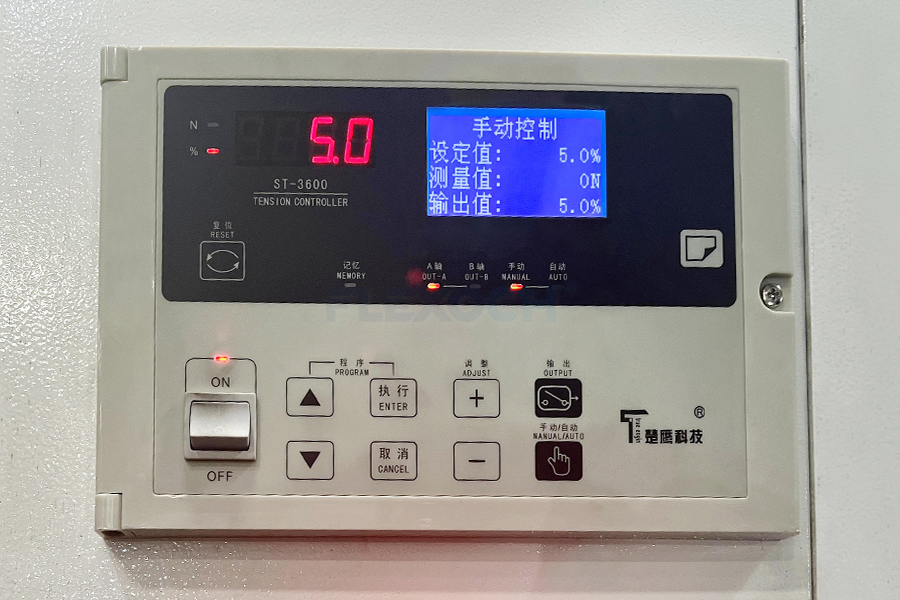
Tension Control System
2. Process and Material Synergy
Process parameters and material compatibility directly influence speed limits for stack flexo printing machine. Using low-viscosity, fast-drying inks (e.g., UV or water-based) tailored to substrate properties improves transfer efficiency. Automation tools like preset printing parameters, reduced doctor blade angles , and automatic registration systems minimize manual adjustments. Material pretreatment, such as corona treatment for plastic films, enhances ink adhesion, while high-line-count anilox rollers and thin digital plates ensure precision without sacrificing speed.
3. Streamlined Workflow Management
Reducing non-productive time is critical for stack flexo printing machine. Implementing rapid plate-changing systems and standardized tools slashes job changeover durations. Pre-installing plates and inks on backup machines enables seamless transitions between orders. Real-time defect monitoring via online inspection systems and preventive maintenance prevent unplanned downtime. These measures maintain continuous high-speed operation while lowering waste rates.
4. Operator Training and Innovation
Skilled operators are essential for sustaining high-speed production on stack type flexo presses. Regular training on emergency protocols, rapid calibration, and simulated fault scenarios improves team readiness. Collaborating with manufacturers to integrate advanced technologies overcomes traditional mechanical constraints. Data tracking systems analyzing post-speed-up metrics further guide iterative improvements.
Video Introduction
5. Cost-Speed-Quality Equilibrium
Speed gains in stack flexo press must align with cost-effectiveness. While UV curing accelerates drying, its energy consumption requires evaluation; servo motor upgrades demand ROI analysis. Prioritizing low-cost optimizations (e.g., parameter adjustments, preventive maintenance) before capital investments ensures balanced progress. Staged testing identifies equipment speed thresholds, preventing efficiency losses from rising defect rates.
Conclusion
Achieving higher speeds in flexographic printing is a multidimensional endeavor. Stability from hardware upgrades, efficiency from process-material synergy, and continuity from workflow and workforce optimization collectively break traditional limits. The ultimate goal is not unchecked speed but a sustainable equilibrium among quality, cost, and productivity.
Post time: May-23-2025