The rapid development of the flexible packaging industry has ushered in an unprecedented wave of innovation in plastic film printing technology. From food packaging to industrial films, the demand for high-precision printing on BOPP, OPP, PE, CPP, and other plastic substrates (10-150 microns) continues to grow, driving flexo printing technology to push its limits. Ci flexo printing machines with their exceptional print quality, high production efficiency, and outstanding environmental performance, are reshaping the landscape of plastic packaging printing.
● Production Efficiency: Revolutionary Improvements Through Intelligence
Modern ci flexo printing machines strike an ideal balance between speed and stability. Models featuring intelligent drying systems can achieve high-speed printing at up to 250-500m/min while ensuring instant ink curing, effectively resolving common issues like ink offsetting and smudging. Modular design principles make plate and color changes quicker and more convenient, significantly reducing downtime. The application of intelligent tension control systems enables the machines to automatically adapt to films of varying thicknesses (10-150 microns), ensuring stable material handling from ultra-thin CPP to thick BOPP.
● Video Introduction
● Color Accuracy: The Core Competitiveness of Flexo Printing
Contemporary ci flexo presses utilize advanced ceramic anilox roller technology, whose superior hardness and wear resistance ensure long-term stable ink transfer performance. Whether it's high-saturation spot color printing or delicate halftone gradients, precise color reproduction can be achieved. Models equipped with enclosed doctor blade systems further enhance ink control, minimizing misting and ensuring consistent color output. The introduction of the central impression (CI) cylinder design allows for more accurate tension control during printing, achieving registration accuracy of ±0.1mm precision—even for double-sided printing, perfect pattern alignment is guaranteed.
● Environmental Advantages: The Inevitable Choice for Green Printing
Amid growing environmental compliance requirements, the eco-friendly nature of flexo printing stands out even more. The widespread use of water-based and low-VOC inks has substantially reduced harmful emissions during the printing process. The extended lifespan of ceramic anilox rollers not only decreases consumable replacement frequency but also lowers overall operational costs. Additionally, ci flexo printing machines are designed with energy-efficient components and optimized workflows, further reducing their environmental footprint while maintaining high productivity.
● Future Outlook: Advancing Toward Intelligence and Customization
With the deepening of Industry 4.0, next-generation flexo printers are rapidly evolving toward greater intelligence. Features such as remote monitoring, smart diagnostics, and automatic adjustments are becoming standard, providing manufacturers with more efficient management solutions. Meanwhile, customized models for specialized materials continue to emerge, meeting the growing demand for functional packaging.
From color accuracy to production efficiency, from environmental performance to intelligent capabilities, ci flexo printing machine are setting new industry standards for plastic film printing. These technological breakthroughs not only enhance print quality but also propel the entire packaging industry toward greater efficiency and sustainability. In this era of abundant opportunities, staying ahead of the latest trends in flexographic printing technology is key to securing a competitive edge in the future.
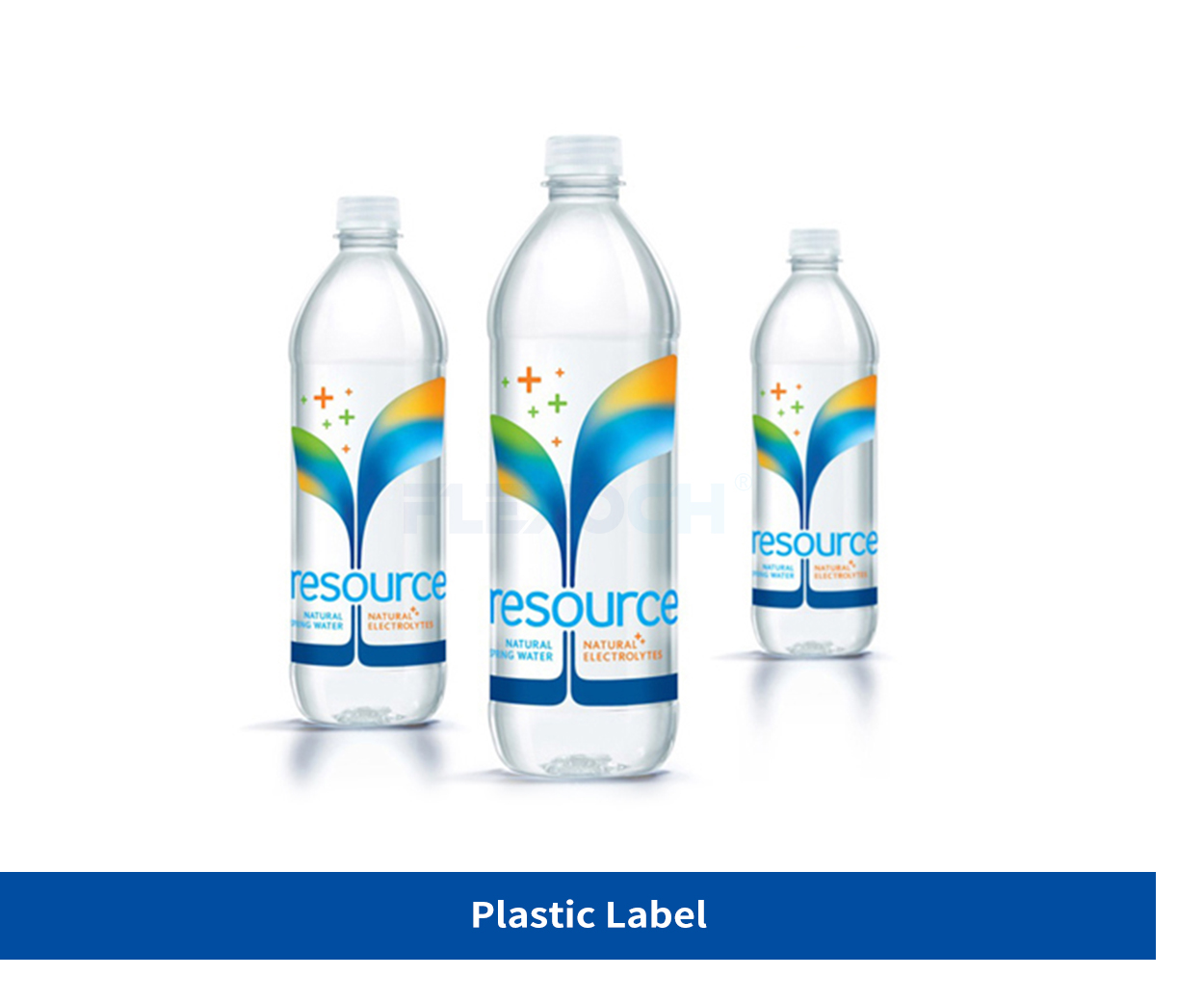

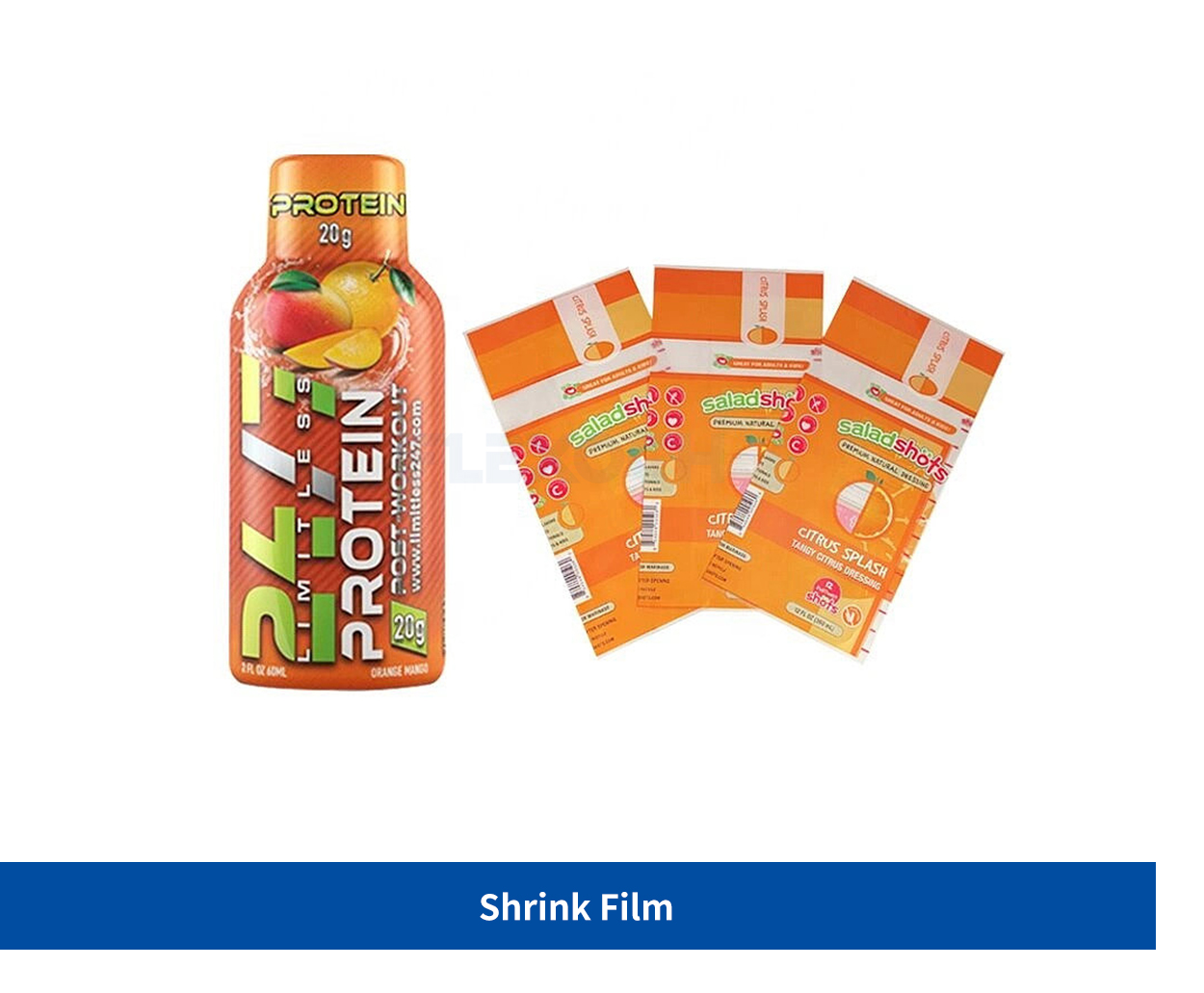
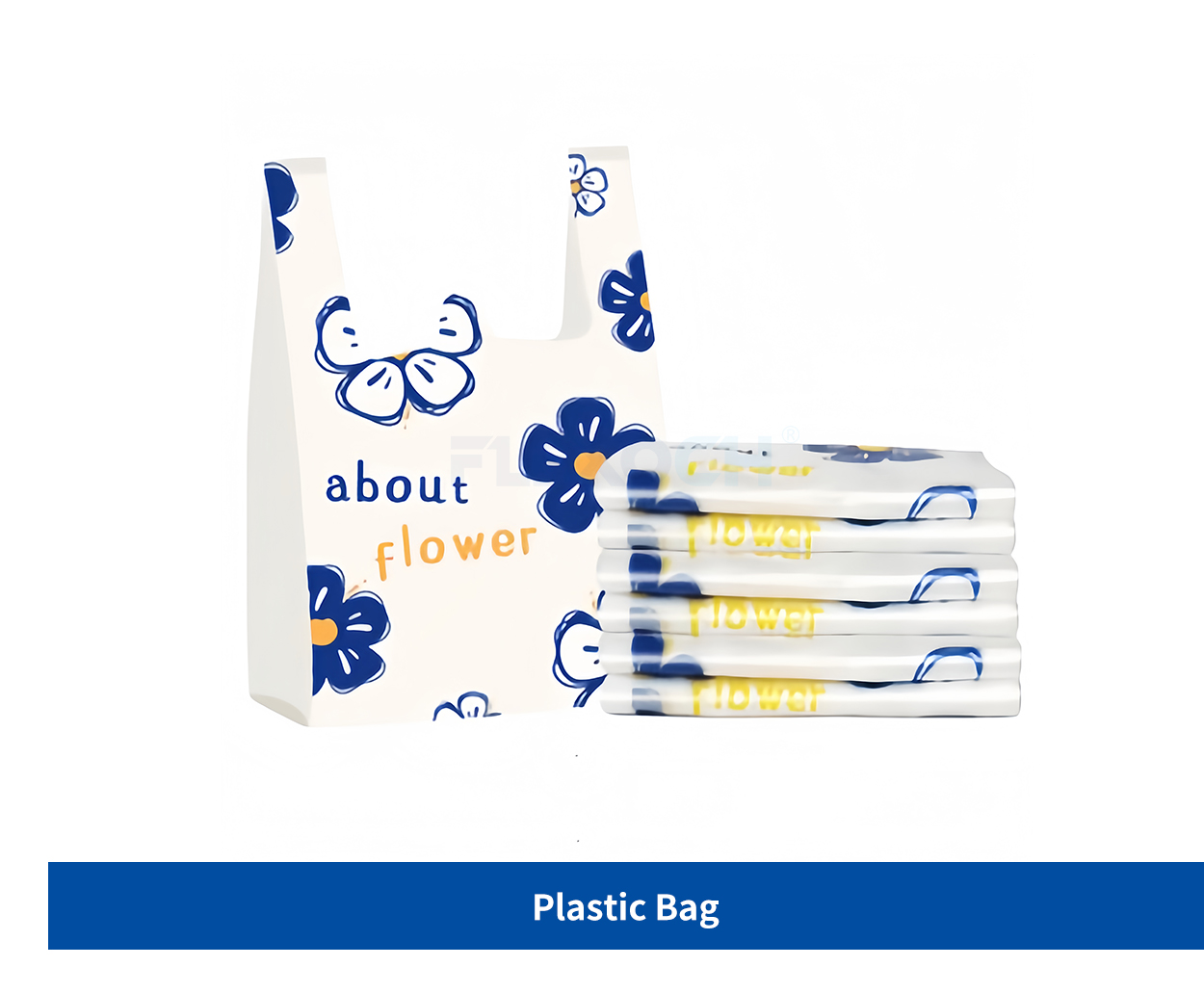
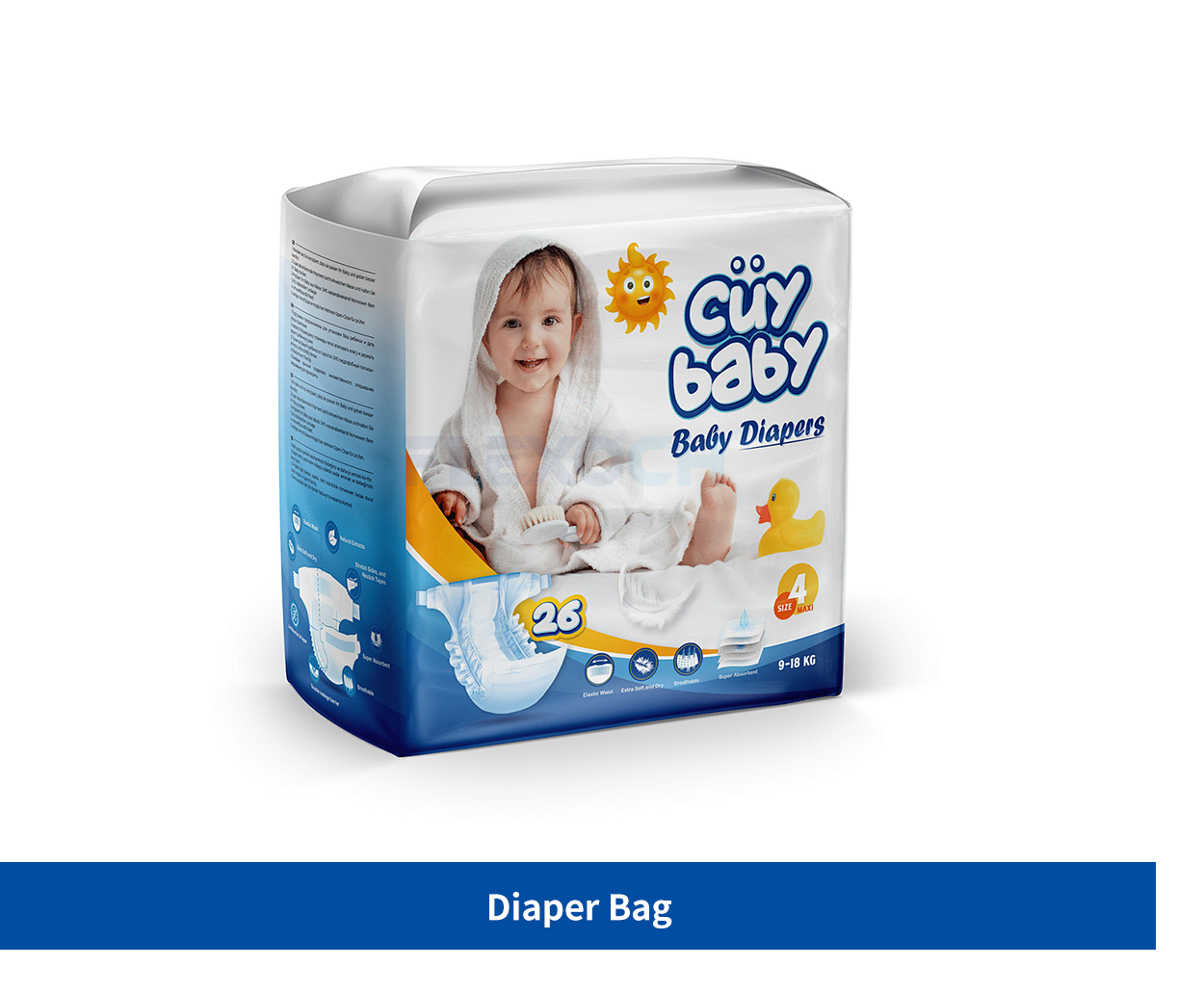
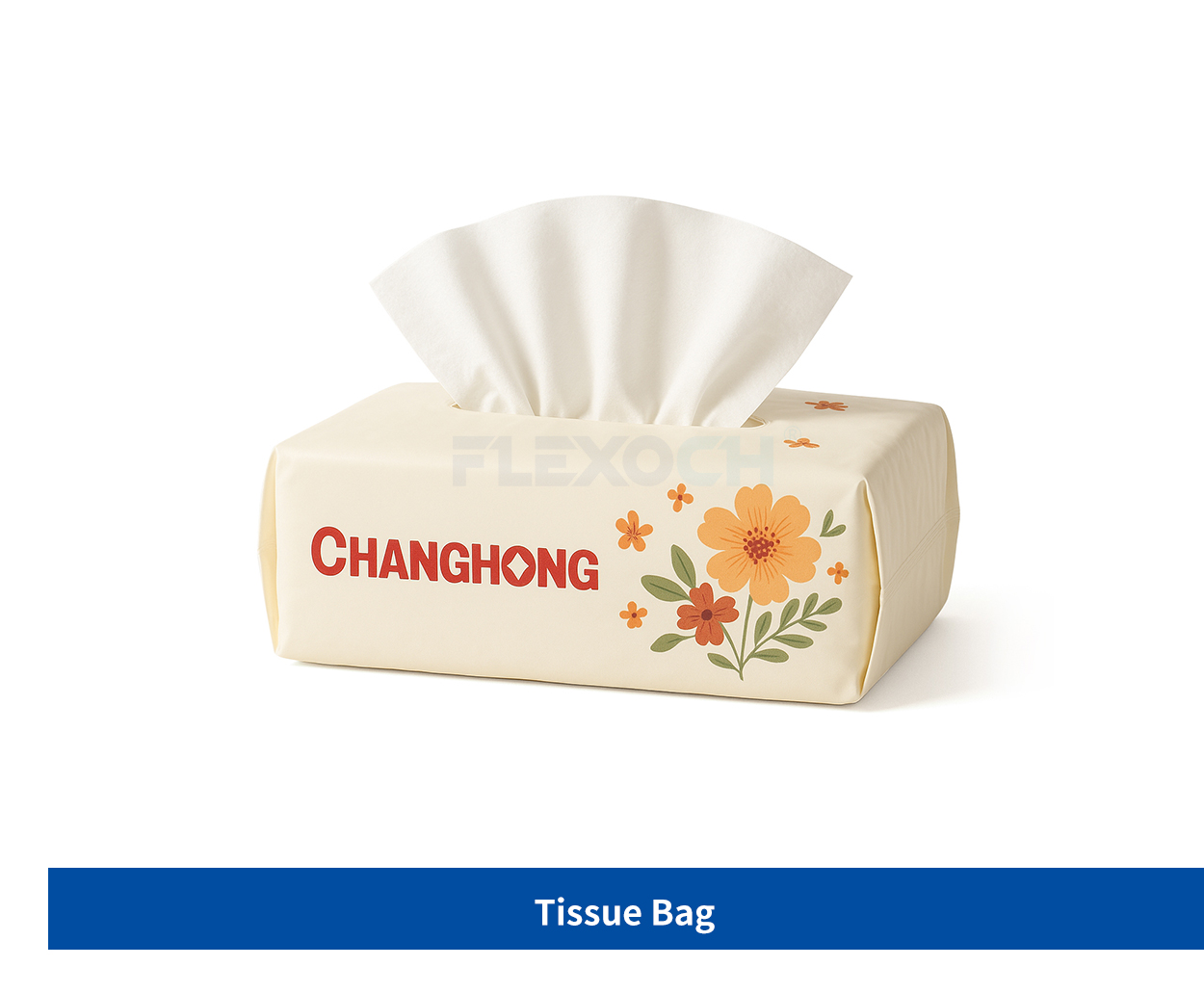

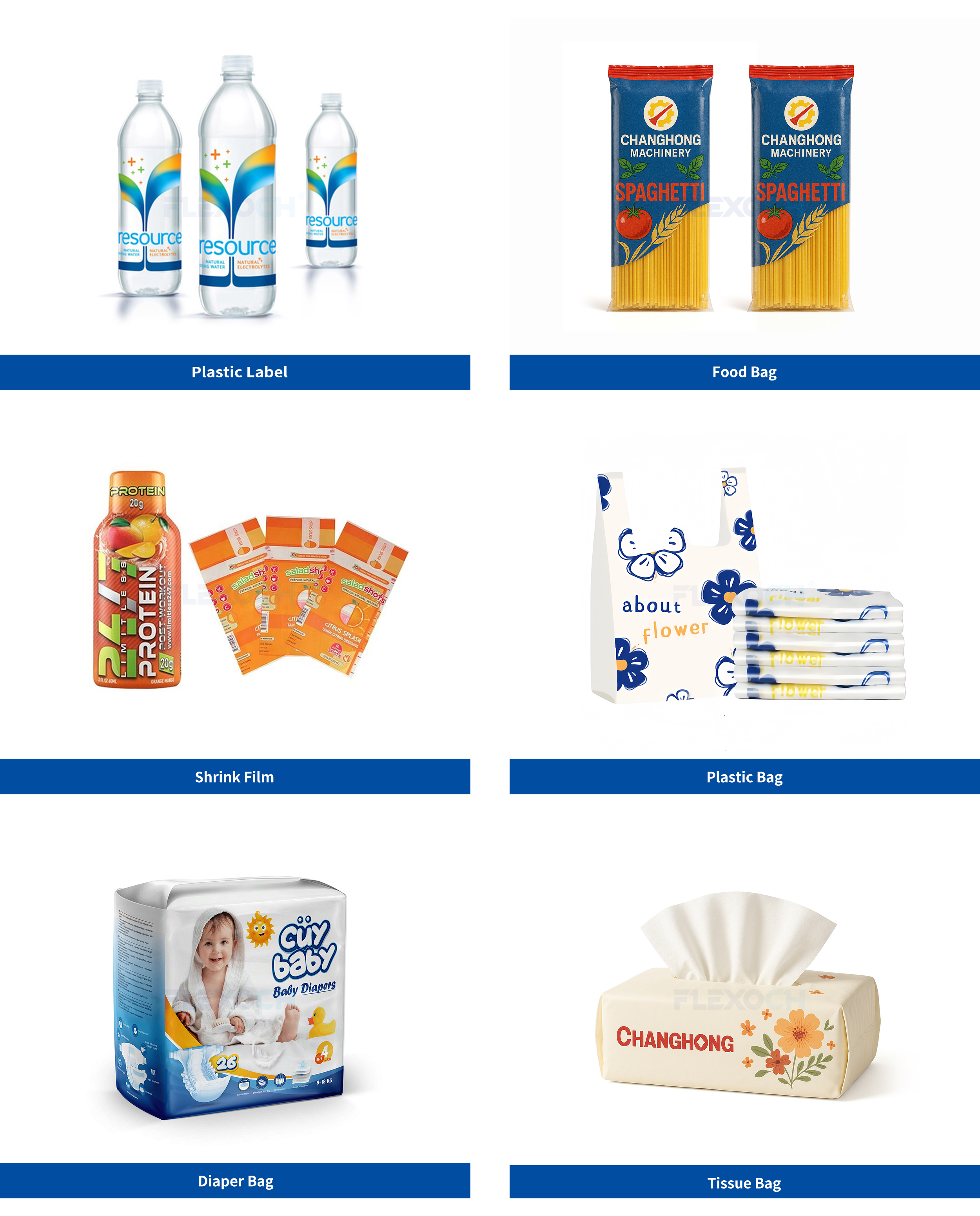
Post time: May-16-2025