In the fast-evolving world of packaging printing, choosing the right flexographic press can make all the difference in productivity and competitiveness. Whether it’s the versatile multi color stack flexo printing machine or the precision-engineered central impression (CI) flexo printing machine, each configuration offers distinct advantages tailored to different business needs.
For operations prioritizing flexibility and cost-efficiency, the stack printing flexo machine delivers a modular, scalable architecture. Its segmented print stations enable rapid reconfiguration for short runs or specialty processes like cold foil application, while independent units reduce lifecycle costs through simplified maintenance and phased upgrades. Operators adjust ink settings, swap plates, or integrate components (e.g., high-resolution anilox rollers) seamlessly between jobs, eliminating full-line downtime.
The printing unit's stacked configuration combines precision engineering with process versatility. Servo-driven registration control ensures ±0.15mm accuracy across challenging substrates, from stretch-sensitive films to rigid laminates. Interstation drying modules prevent ink migration on non-porous surfaces,ensuring uniform output quality across entire production runs.
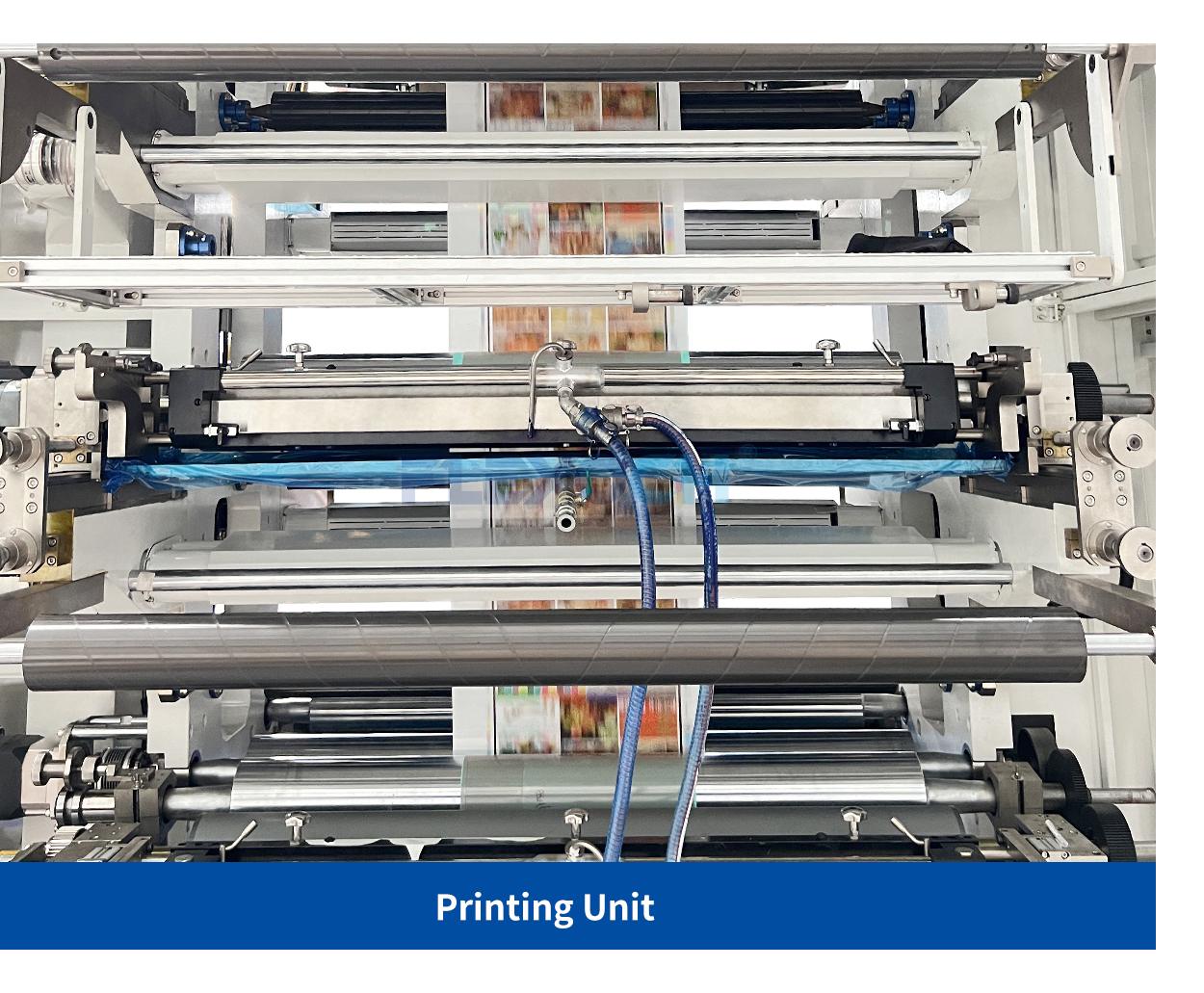
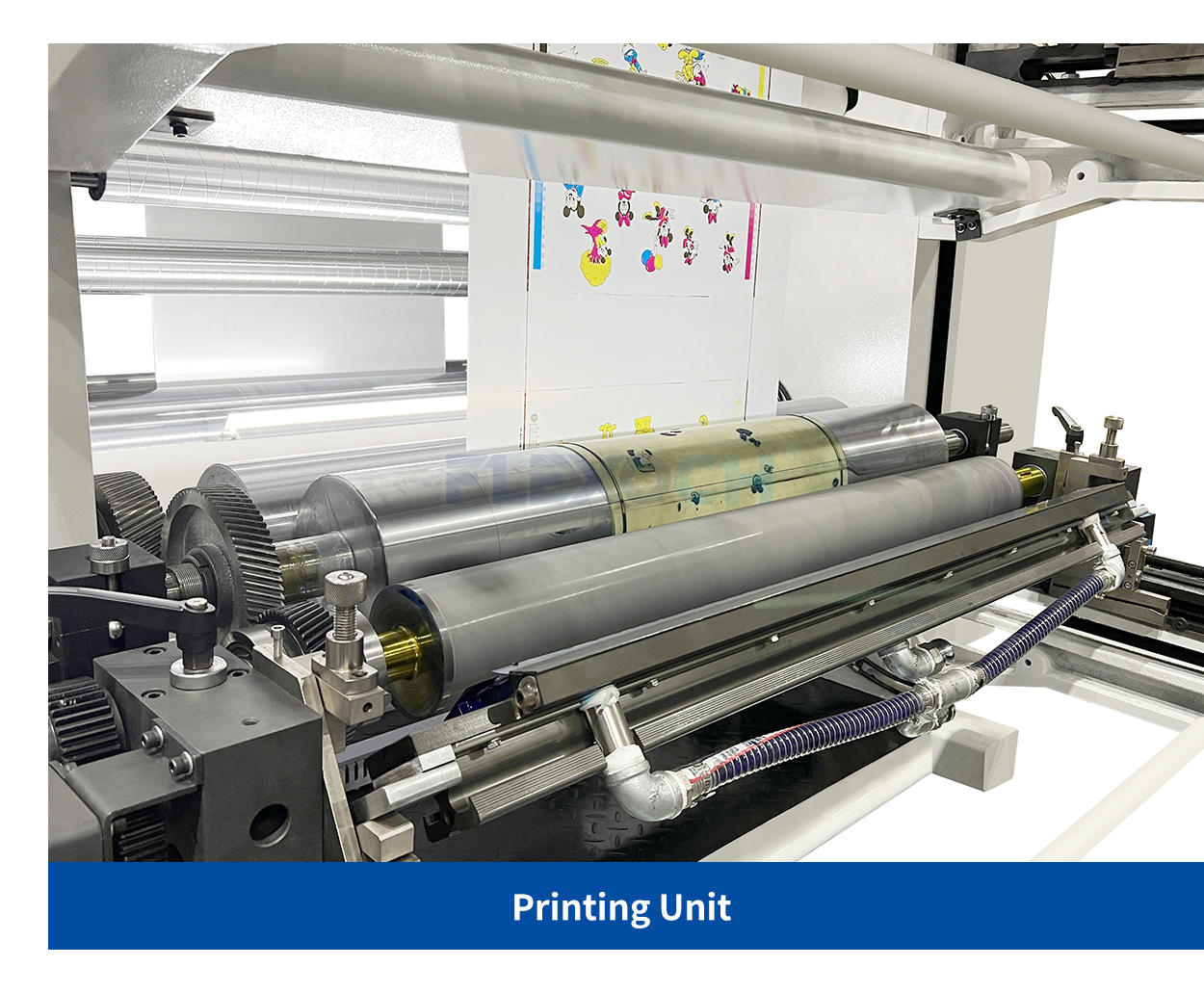
Building on the operational flexibility of stack flexo printer, ci flexo technology takes precision engineering to its logical extreme for high-volume production. The massive precision-ground impression cylinder serves as the heart of the system, maintaining constant tension across stretch-sensitive films and thin substrates that would distort on conventional presses. This design inherently synchronizes all print stations around a single circumference, eliminating cumulative registration errors during high-speed runs—a decisive edge when reproducing flawless gradients, micro-text, or exact brand colors.
The core competitive advantage of CI flexographic printing press lies in their integrated printing unit design. The impression rollers of each color station are precisely aligned with the central drum, ensuring uniform pressure for sharper dot reproduction.Unlike stacked configurations where substrates travel between independent units, the ci flexo press's wrap-around web path significantly reduces material fluctuations, delivering tighter registration tolerances(±0.1mm) for premium label and flexible packaging applications.
This design represents a trade-off in flexibility: while stack flexo printer allow for quicker station reconfiguration, CI systems specialize in delivering unmatched stability for long production runs - making them the ideal choice for standardized, high-volume production demanding industrial-grade repeatability.
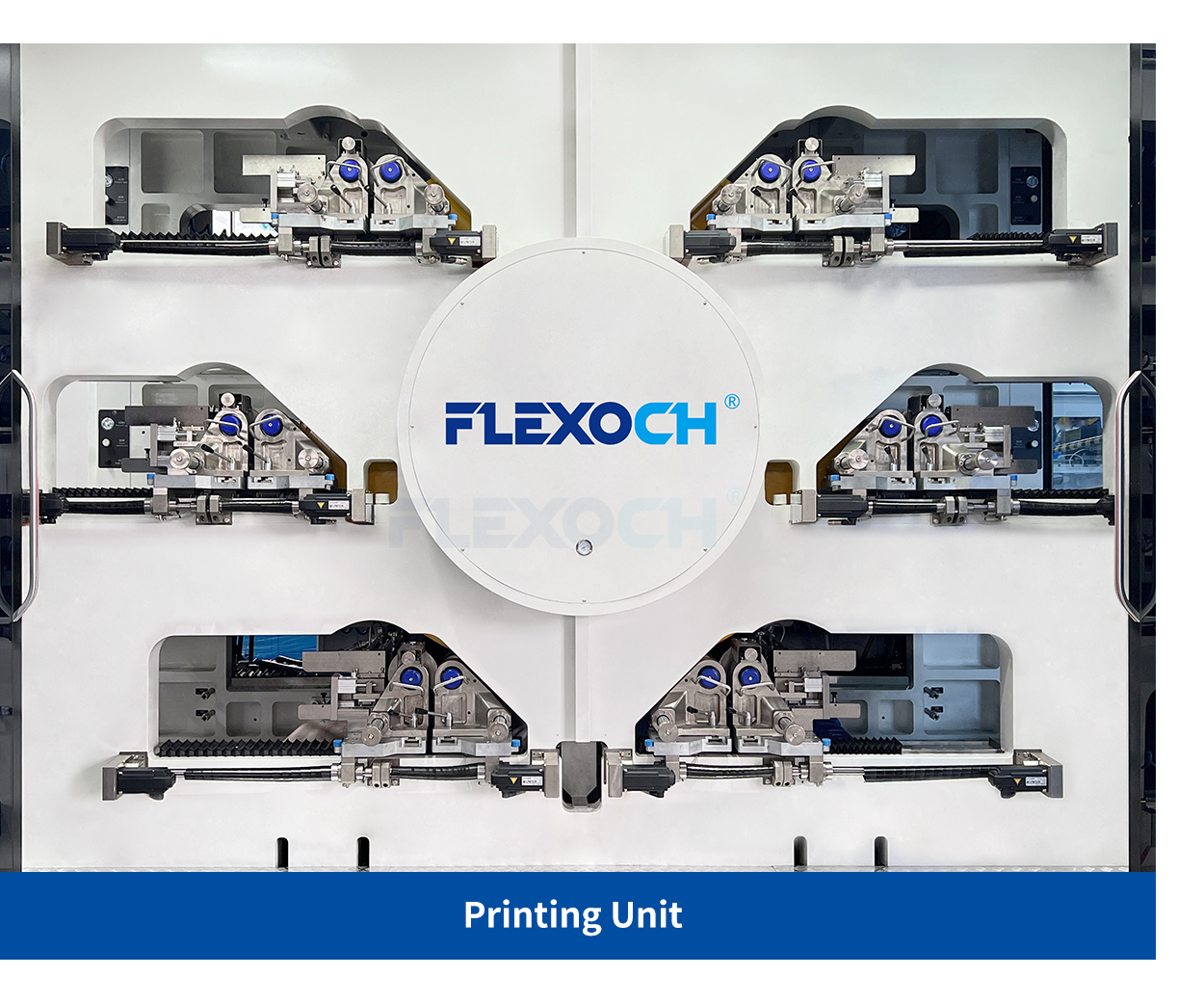
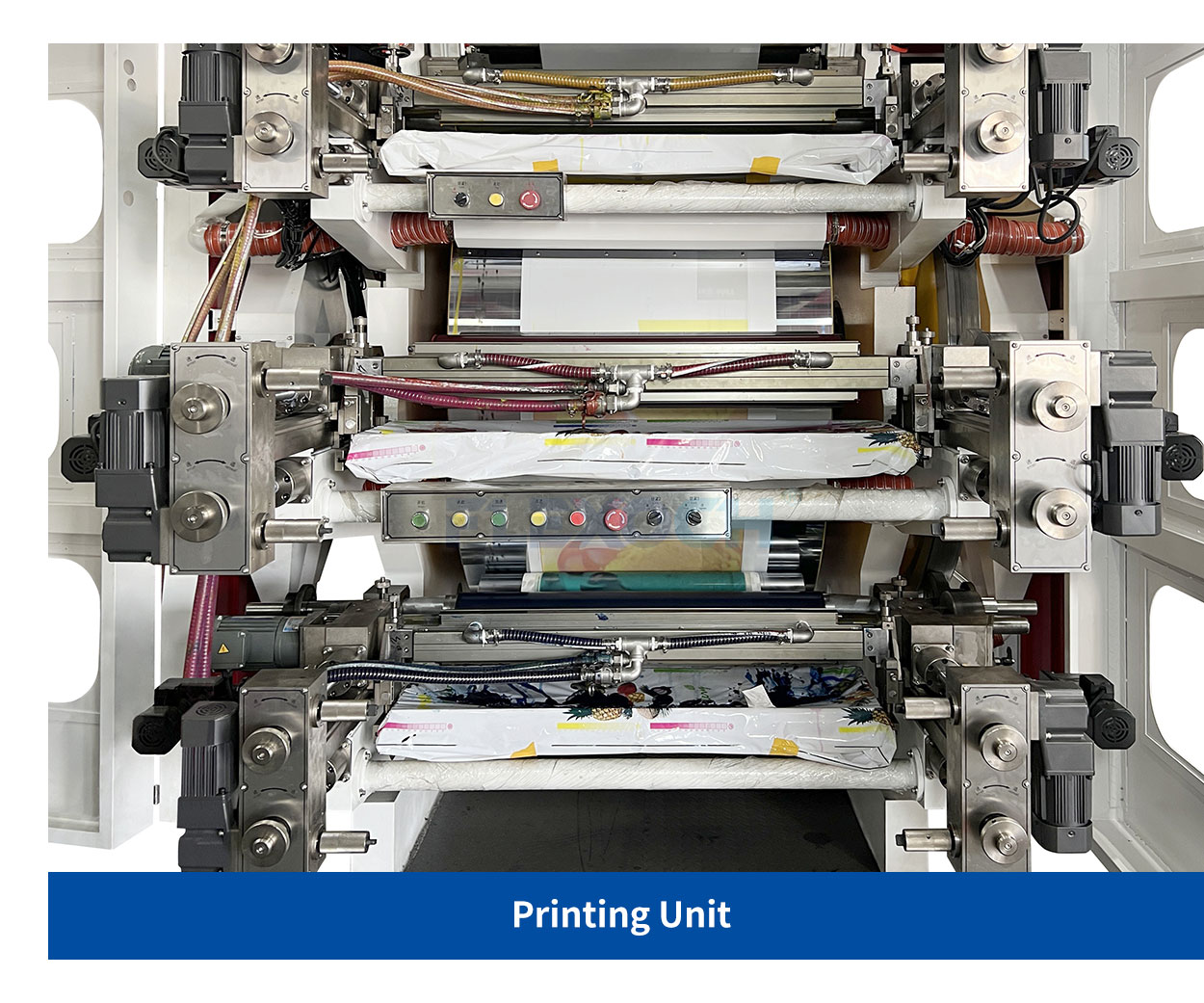
Before making your decision, consider these key questions: Does your workflow consist of diverse short runs or high-volume standardized jobs? Is your technical team more comfortable with segmented setups or integrated systems? Are your customers more cost-driven or quality-focused? The answers likely lie in your day-to-day operations. Whether you opt for the expandable stack flexo printing machine or the high-performance ci flexographic printing press, the right choice hinges on aligning the machine’s strengths with your business —striking the perfect balance between quality, efficiency, and cost.
● Printing samples
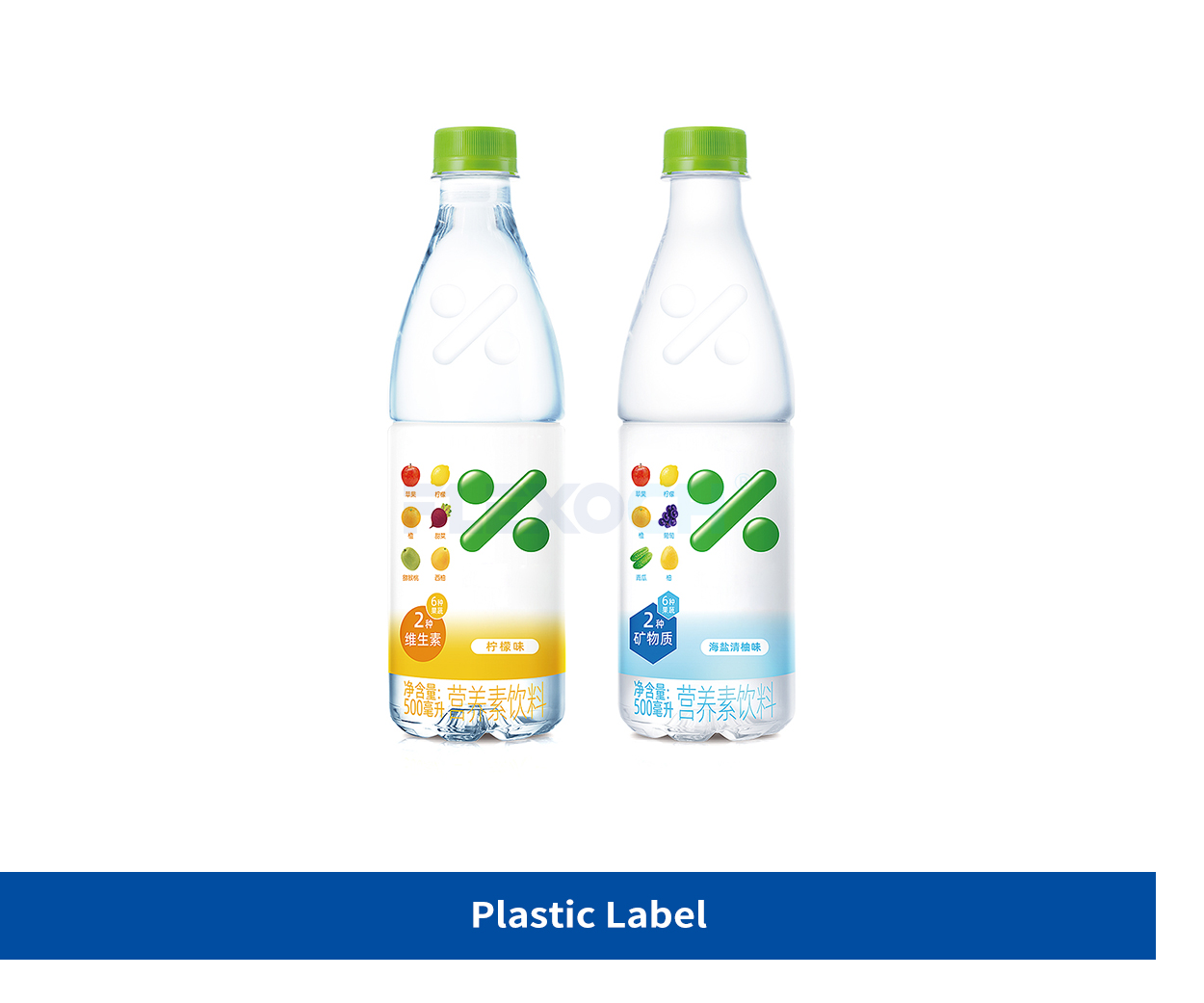
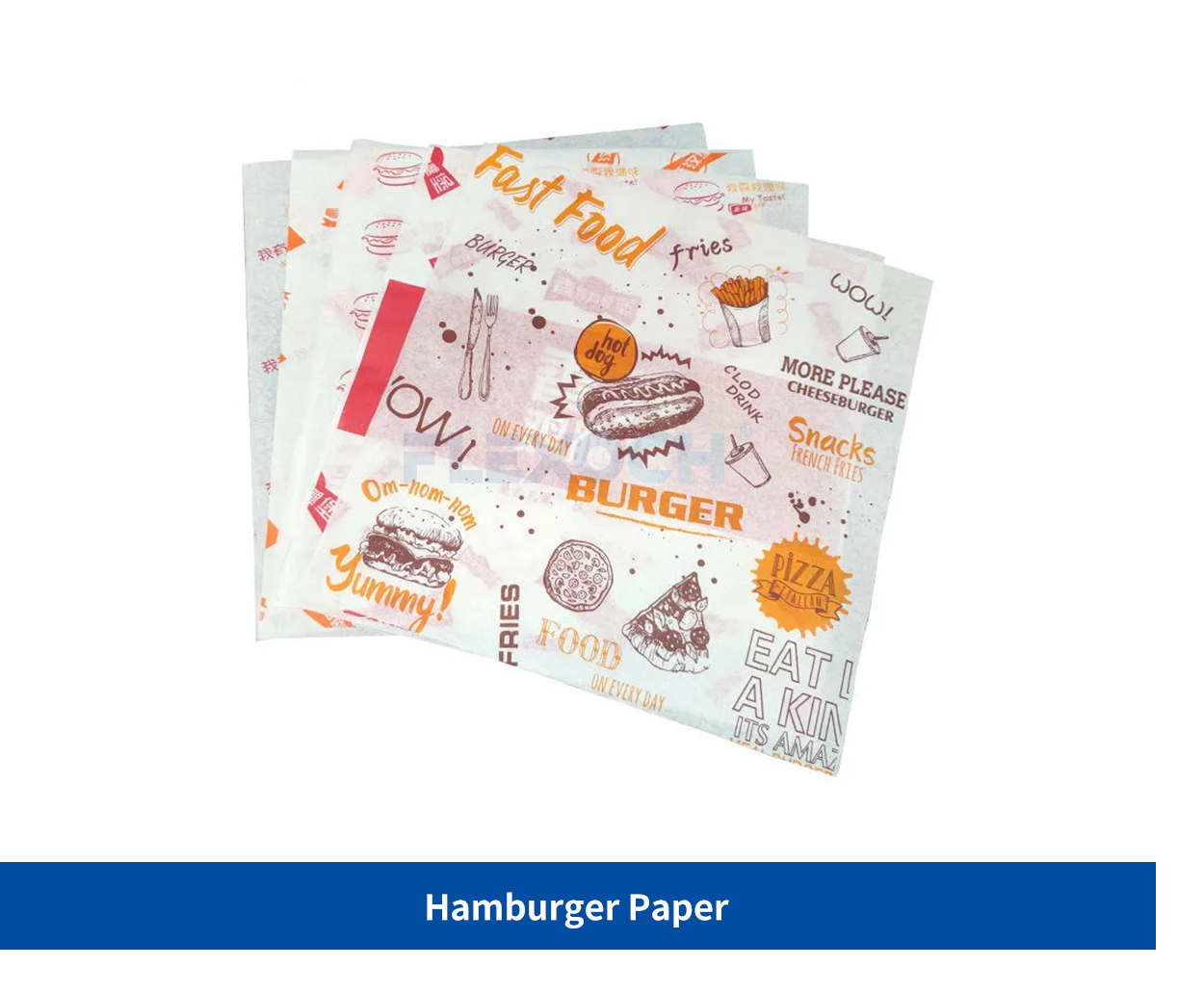
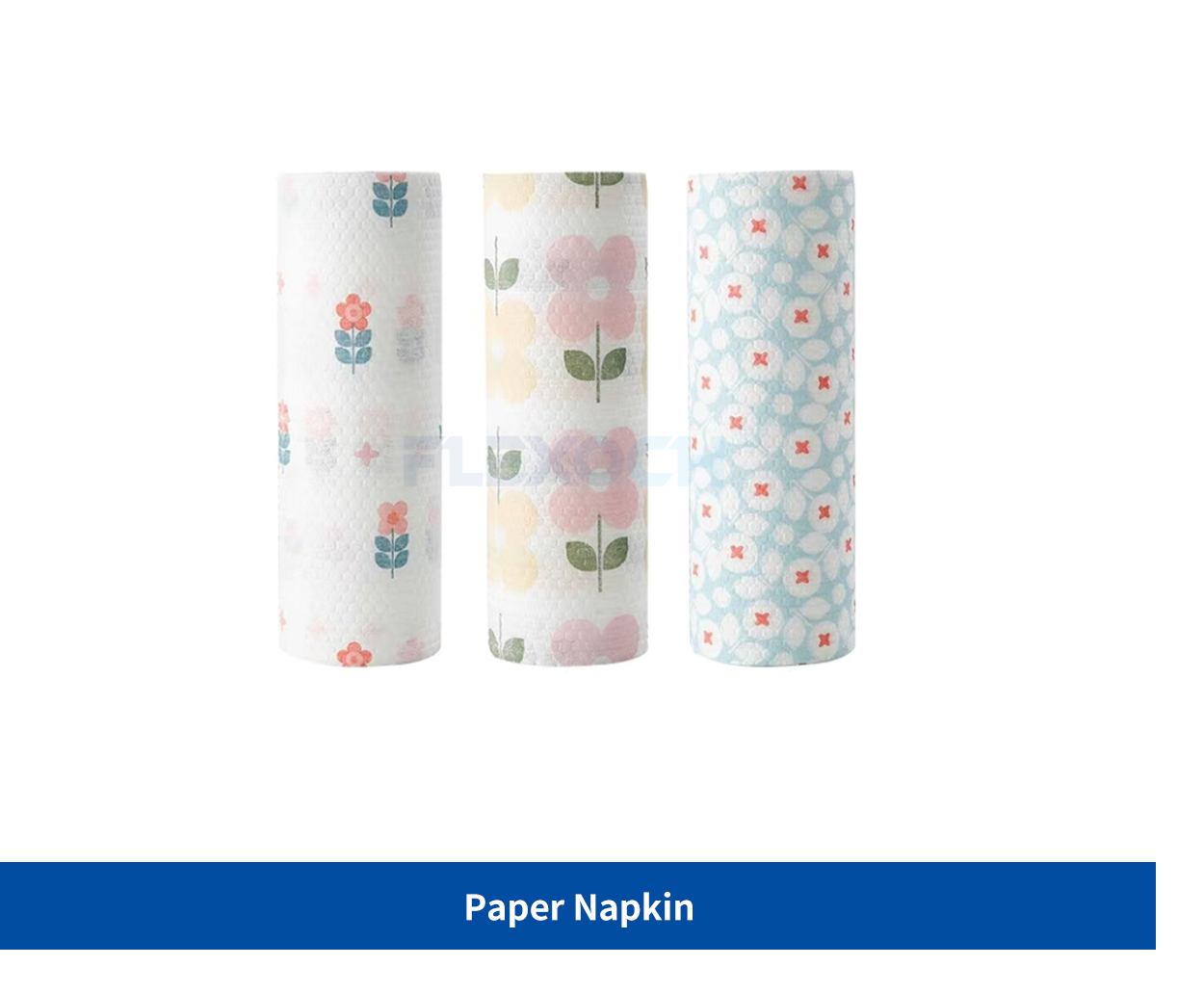
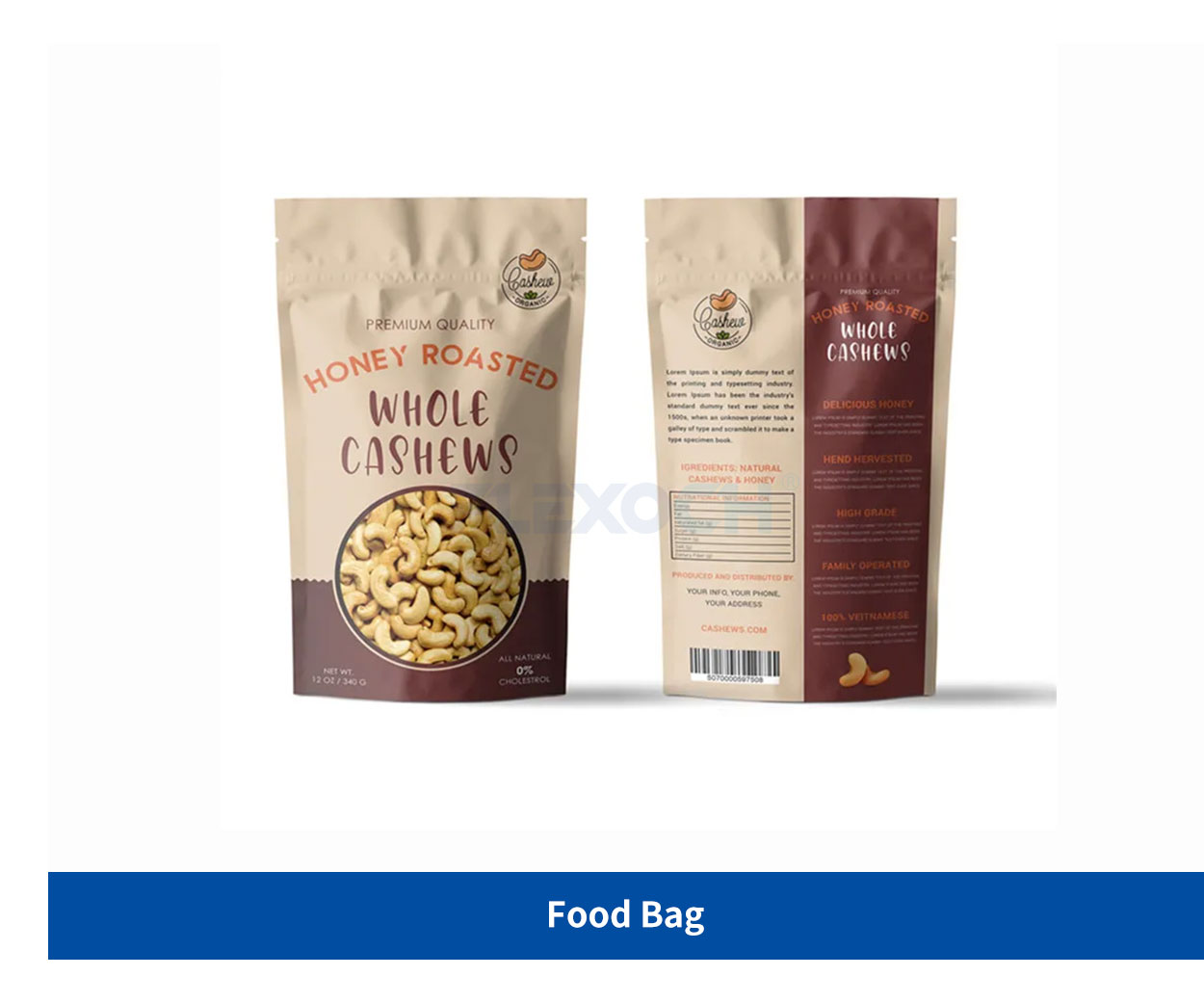
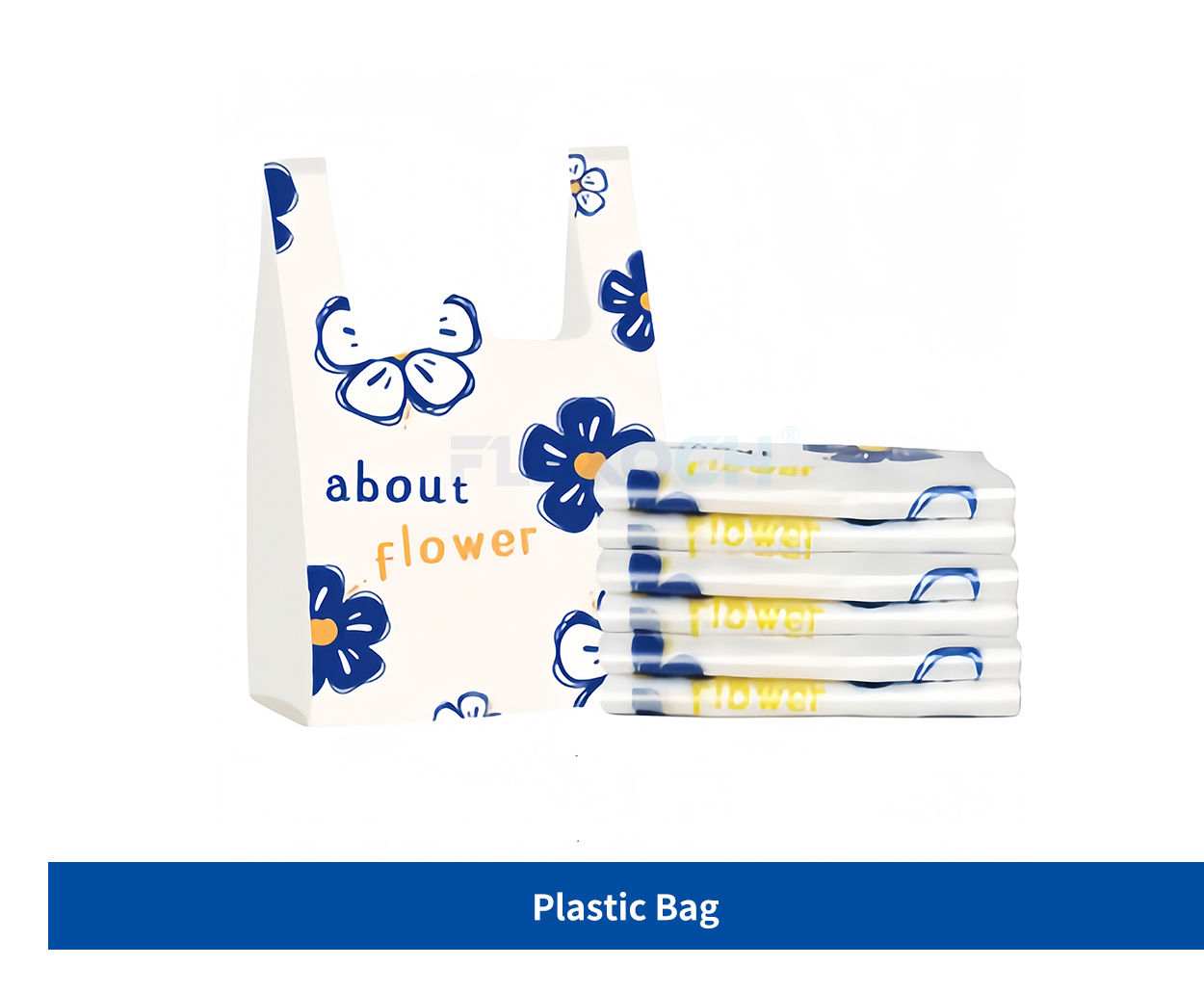
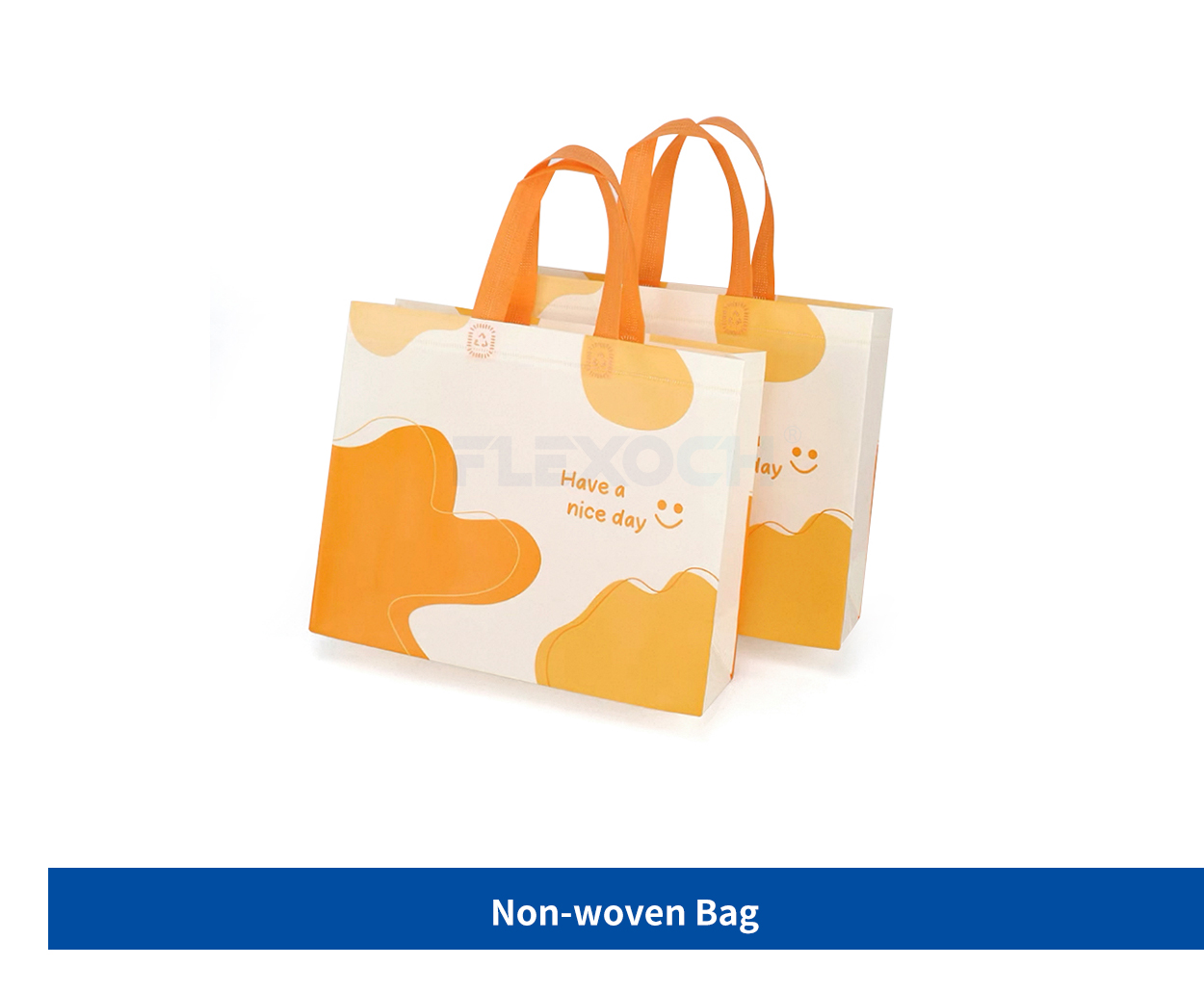
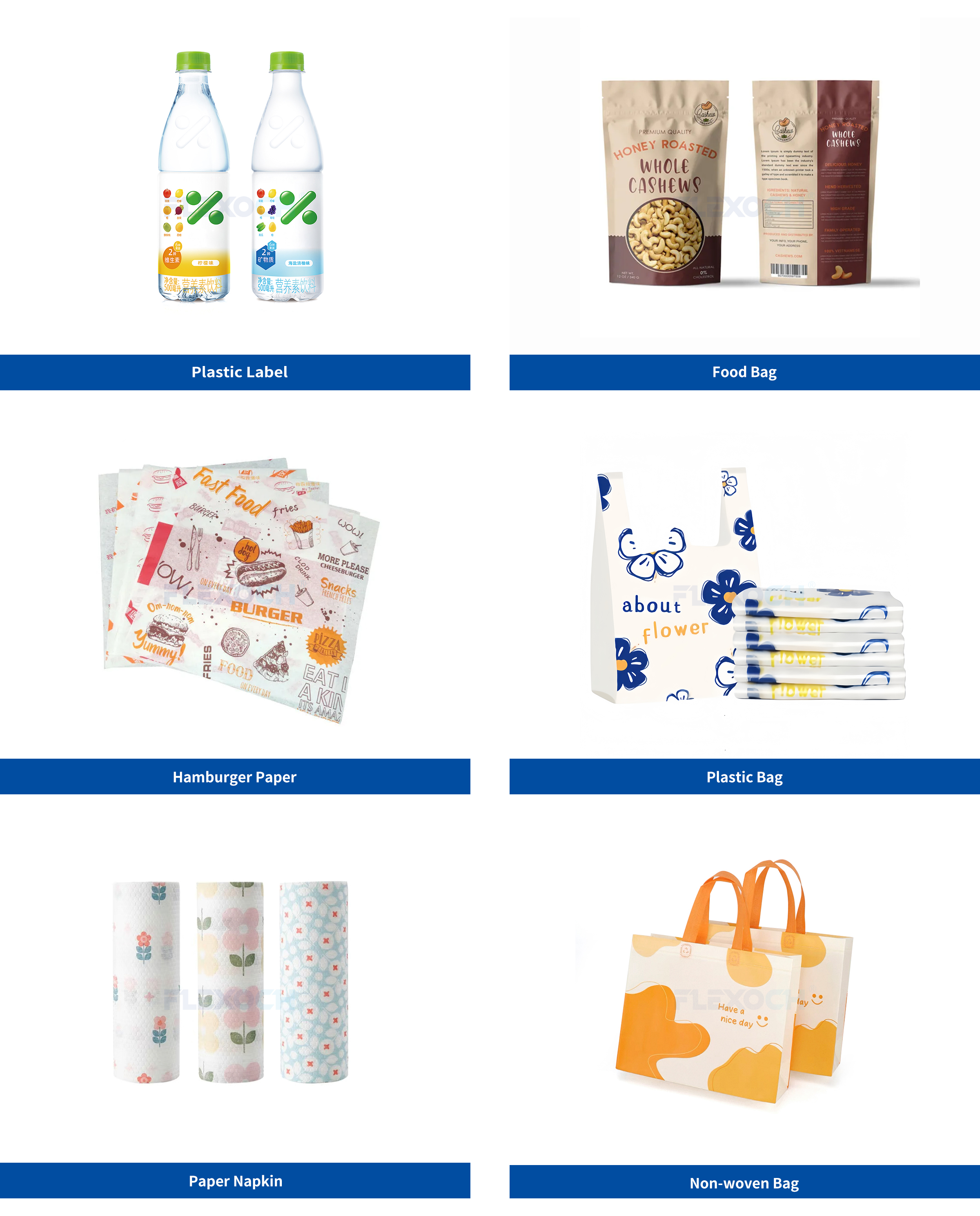
Post time: May-10-2025